A leading manufacturer of high-quality bath/shower tubs and wash basins made from steel and enamel has asked for a lubrication system that perfectly fits this very special and demanding production process – and we have delivered on all counts! The Swiss company now enjoys the benefits of our very own spray concept EOS Move.
The system comes into play when a robot loads and retrieves the blanks out of which the tubs will be formed. It was required to perfectly blend in the existing automatization infrastructure and be able to realize a variety of spray patterns with minimal set-up time.
Movable spray unit
The EOS Move lubrication system is based on our tried and tested EOS-X short construction version, but reverses the operating principle: it’s not the blank that moves through the lubricator – it’s the spray bar that slides across the material and applies the lubricant from above and below. The customer’s specifications require this process step to be completed within 15 seconds from inserting to removing the blanks, the sizes of which vary from 500 to 1800 mm in width, 800 to 2500 mm in length, and 2 to 2,9 mm in thickness.
Optimal temperature and filtering
The spray unit rests on a solid base frame and moves back and forth with the help of guiding rails and a guiding carriage. The casing of the spray chamber is enclosed all around, the exception being the guide trenches for the blanks. The spray valves are mounted on an upper and lower spray bar and can be easily accessed through sheet-metal coverings. Eckardt applies its widely used two-medium valves of the SD 25 series, which are flanged directly onto the spray bar in order to prevent cable tangle. The back side of either spray bar includes a heating element, allowing for the temperature in the upper and lower valve row to be adjusted separately and the application of different lubricants under perfect conditions.
The lubricator also includes an Eckardt EONA exhaust unit mounted on the frame of the carriage. The mechanical exhaust system creates a negative pressure inside the spray chamber, thereby preventing the oil mist from being released. Apart from the fan, the exhaust unit contains three prefilters, two afterfilters and one final final of the F9 class. A drip tray collects the overspray and retained lubricant which is then returned to the storage container with the help of a pneumatic membrane pump.
Individual settings, unlimited
The EOS control software provides a wealth of setting options for all relevant spray parameters, e.g. separate regulation of oil pressure and spray air for the upper and lower spray bar, seamless adjustment of oil temperatures, continuous lubrication or skipping of blanks, and many more. The spray areas for the front and back side of the blanks can be determined at the click of a mouse, based on the exact proportional mapping of blank sizes and shapes in the software. It is also possible to assign different lubricant quantities to the various spray areas. Modifications to the spray programs can be made during operation.
Following extensive functional testing at the Eckardt production site in Bretten the EOS Move spray lubricator has found its new home and has taken on its task in further improving the manufacturing process which is already top-notch.
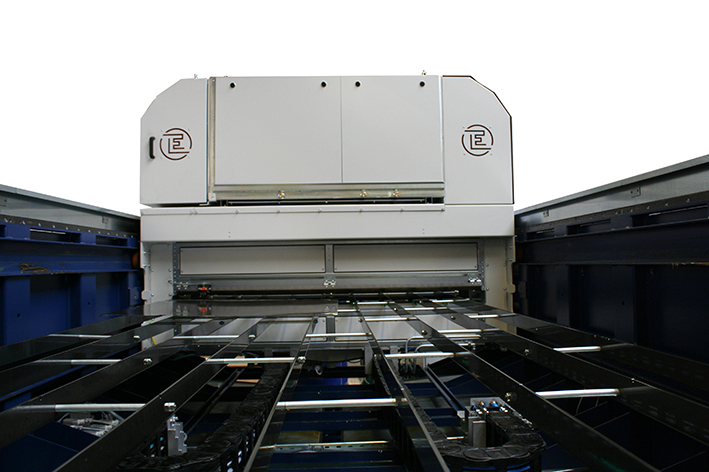
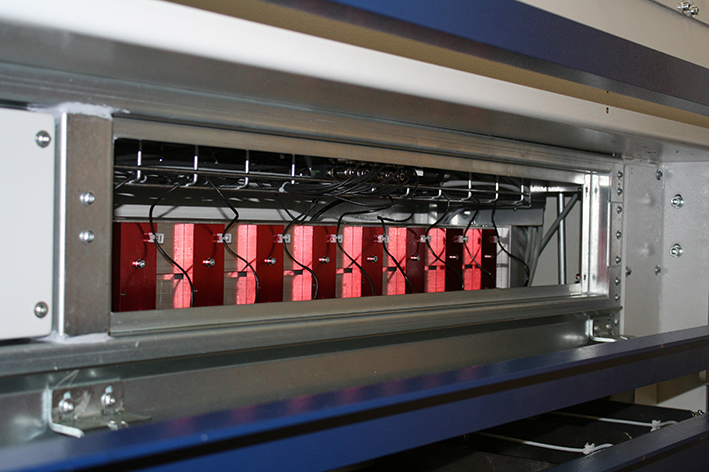