Apply with rollers or spray? Frequent change of oil type? Completely different lubricants and material sizes in play? These questions arise with every process planning. In addition, there are considerations regarding acquisition, consumption and operating costs, wear and maintenance. You often come to the conclusion that “the” solution doesn’t actually exist.
Why not simply combine the best of both worlds? This is what a specialist in stamping and tool technology from Upper Austria is doing with its new press line. The initial plan was to rely entirely on roller lubrication. However, very different application quantities are required for the main type of oil, and the necessary flexibility in adjustment can only be achieved by spraying. In addition, very thin coil thicknesses are processed with a high throughput, for which the spraying variant also offers advantages.
Dual solution for up to 1000 mm material width
With this in mind, we provided the customer with a dual solution in which the roller and spraying systems are positioned directly behind each other. This allows material widths of up to 1000 mm to be processed.
The roller system from our WF-WG series is designed for material thicknesses of up to 10 mm and can be operated with interchangeable rollers. They are equipped for different application widths so that the lubricant does not have to be fed across the entire width of the machine if the material is significantly narrower. The rollers for the next process step can be changed particularly quickly via lifting cylinders at the top and bottom. To do this, the lubricator mounted on a telescopic arm is simply pulled out of the process line.
The spraying unit consists of the EOS-X model from Eckardt. It is designed for strip thicknesses of up to 2 mm. 10 standard SD 25 spray nozzles are installed at the top and bottom of the spray chamber. The medium to be sprayed is swirled with air in the nozzle and applied as a spray mist. In this way, the required coating thickness can be guaranteed with process reliability. An extraction unit is positioned above the spray chamber. The excess solid components in the oil are collected in a tray in the chamber and discharged for recycling.
Control center for three types of oil
The EDS dosing system from Eckardt stays on top of which oil is required when and in what quantity. It is set up for three different types of oil, two for the roller oiler and one for the spray oiler. Different width spray strips can be preselected for the latter: 200, 400, 600, 800 and 1000 mm. For application in the spray system, the corresponding number of nozzles is then activated, which are aligned at the optimum distance from the material passing through in order to largely avoid overspray.

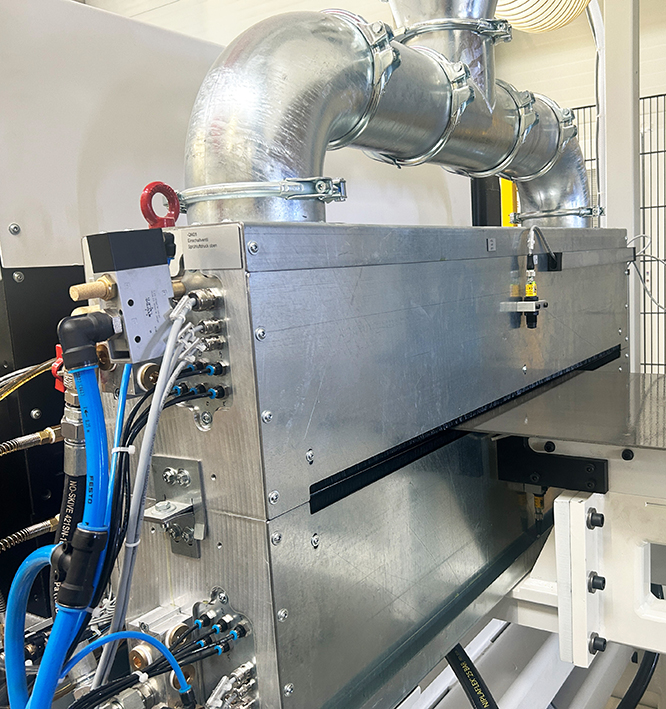
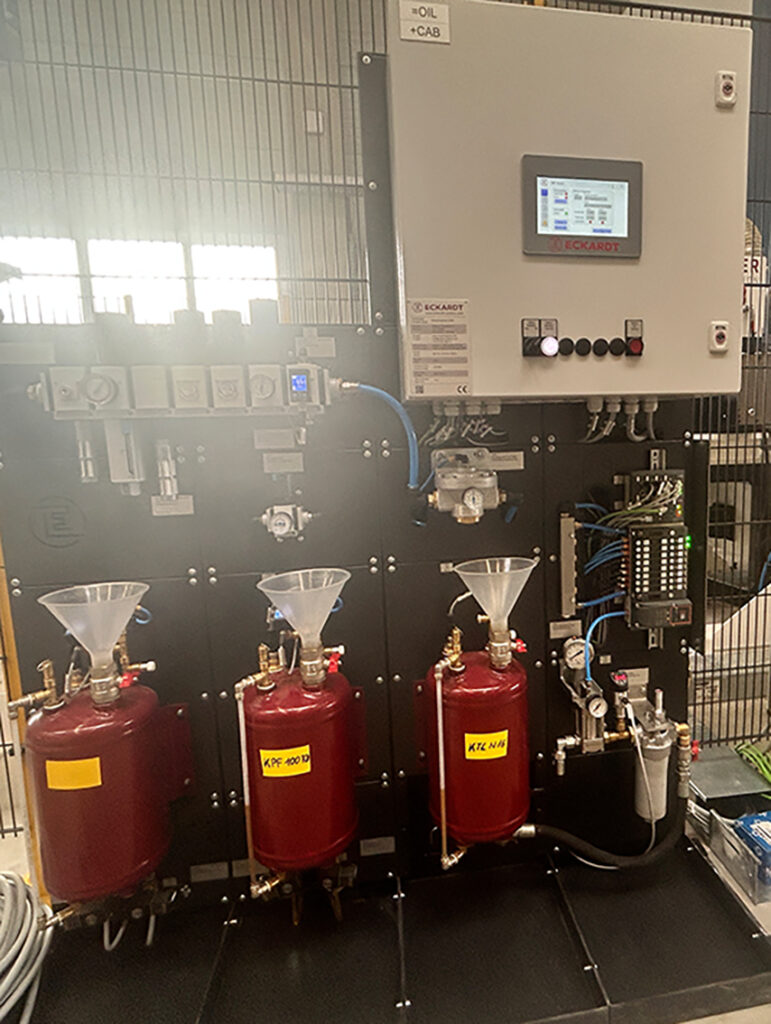